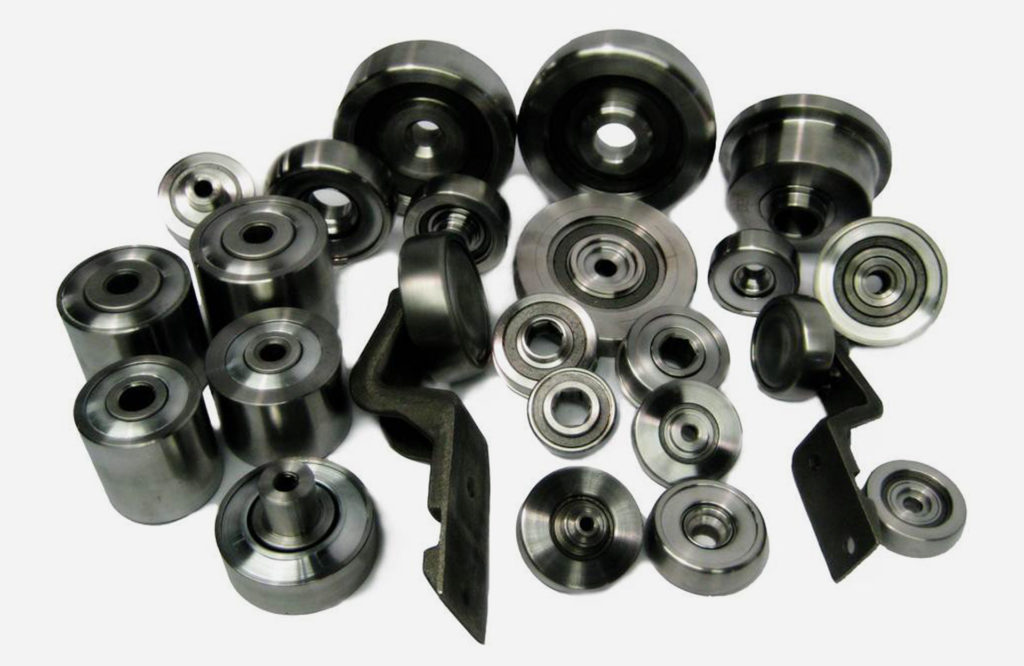
CSL has proven to be a great lubricant for nearly all conveyor systems. Overhead systems, inverted systems, enclosed track systems, power & free, gravity conveyors, roller turn rolls, track rollers, hex bore bearings, etc. can all be lubricated with CSL. The benefits are often amazing! The first big benefit is lower drag on the system. Lower drag means less stress on the links, pins, gearbox, drive motor, and roller turn rolls. Those components may also last longer and energy usage (your electricity bill) will be lower!
In some applications, like paint lines, other benefits are realized. Unlike oil or grease, CSL cannot and will not drip. Newly painted parts will not be ruined by oil dripping on them! No more scrapping defects or stripping & repainting parts due to drips.
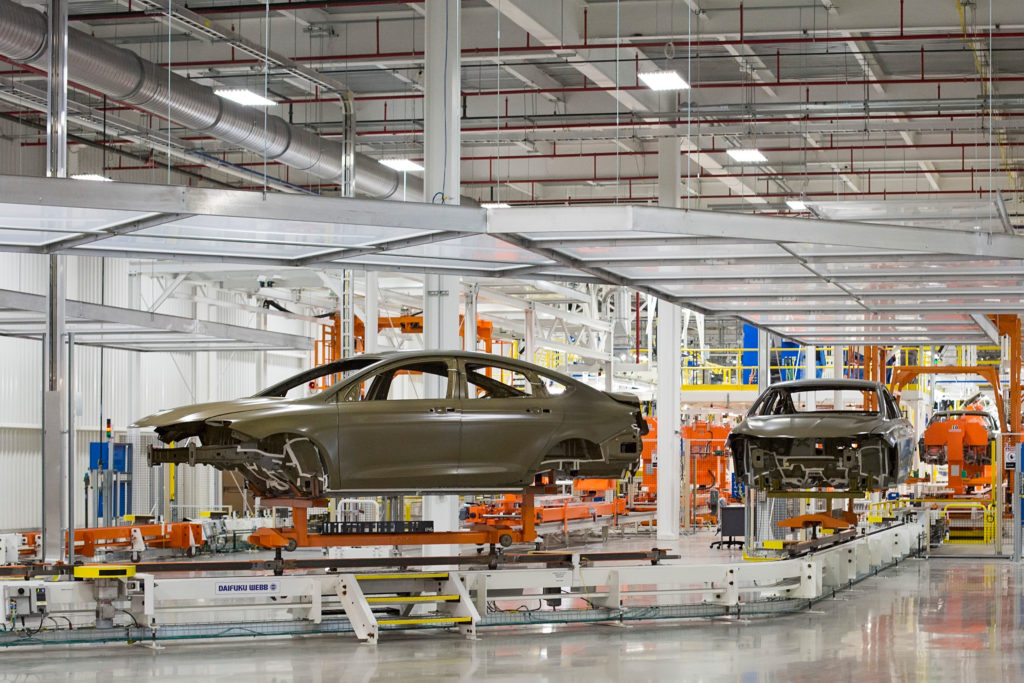
In conveyor systems that are not processed with CSL, auto-lube systems are often used to provide some re-lubrication for trolleys that have dripped out oil due to high temperatures. Most often, these systems require the trolleys to be open on at least one side. Airborne contaminants can quickly clog up the trolleys, sometimes causing trolleys to drag along the track creating a flat spot on the wheel, wear on the pins & links, chain stretch, and even worse, causing excessive ware on the rail!
Trolleys processed with CSL are shielded and auto-lube systems are no longer necessary. With CSL the facility will look, and even smell, better due to the elimination of oil or grease usage which drip onto parts or the factory floor. Some safety issues may be eliminated as well.
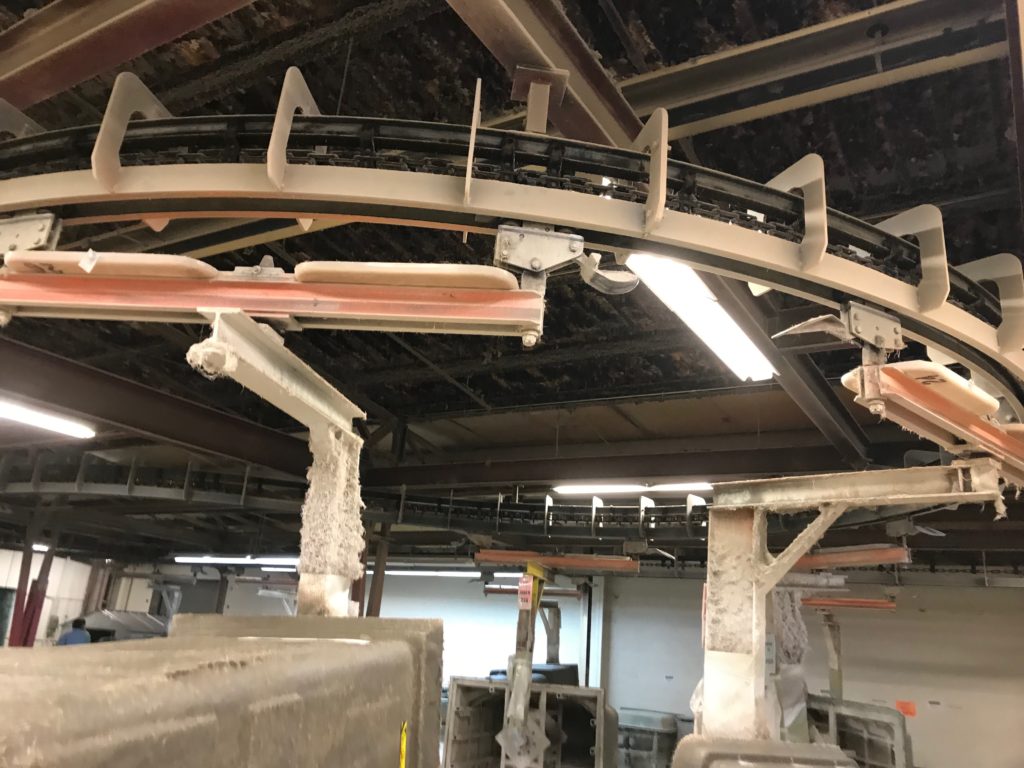
Important Notes:
a. When processed with CSL, conveyor products are “lubed for life”. Auto-lube Systems should be shut down and removed.
b. All conveyor products processed with CSL are engineered to perform from -150°F up to 660°F. 660°F being a continuous rating, CSL has a practical limit of 1200°F with very slow degradation over time.
c. Trolleys must be processed with CSL prior to mounting on the arm or installation of shields. UTA has special arrangements with several conveyor manufacturers to accommodate this requirement. Because of this, it is usually required that UTA supply the whole package of trolleys with CSL. Equivalent replacement for original equipment is typically not problem.
d. Wheels & Hex Bore bearings should be processed with CSL before shields are installed. It is often more convenient for UTA to supply the whole package of wheels and CSL.
e. Roller Turn Rolls are only available as complete products processed with CSL. UTA can offer a wide range of standard and custom designed Roller Turn Rollers processed with CSL.
f. UTA does not install conveyor products or systems.
Applications
Paint Lines & Powder Coat Lines
CSL processed trolleys will roll with little drag. This helps the pins, links, drive motors, and gear boxes of the conveyor system last longer. It will also reduce energy consumption! With the absence of liquid lubricants in the trolleys, there will be no drip and thus fewer defective parts due to “fisheye” or other paint related defects. CSL processed trolleys will be shielded front and rear helping to keep the paint spray or powder dust out. CSL processed trolleys easily handle the temperatures associated with the curing ovens.
Food Conveyors
Whether the product is being baked, smoked, or chilled, CSL processed conveyor components will handle the temperatures, wash downs (use Stainless Steel where required), or other unique conditions of the food processing industry. CSL is an NSF H-1 certified product.
Packaging
Products from pharmaceuticals to food to nuts & bolts are all serviced through packaging lines. Conditions vary according to the products being packaged. Whether dusty, sterile, clean, hot or cold, lightning fast or very slow CSL may improve the reliability of the line by reducing required maintenance and down time.
Assembly Lines
Whether using power and free systems, hand push trolleys, gravity or live conveyors, assembly interruptions are costly. CSL processed bearings and wheels are “lubed for life”, spin free, and won’t drip or fling grease or oil. Moving product through the assembly line can be smooth and efficient. Work stoppages due to unscheduled down-time become a rare occurrence.
High Heat Applications
Heat treating furnaces, paint curing ovens, baking ovens, and anodizing furnaces can all pose big problems with lubrication systems. CSL can work well at continuous temperatures up to 660°F and short term temperature increases more than twice that high! CSL will not burn in the presence of an open flame! No oil or grease to drip out, no re-lubrication needed.
Low Temperature Applications
Whether your conveyor system is inside a cold storage facility – flash freezing “just baked pizza” or ice cream packaging – or running outdoors between warehouse buildings in Canada, cold temperatures are typically a problem. CSL processed conveyor trolleys and rollers will turn free, at temperatures as low as -150°F, with no additional drag caused by increased viscosity of oil or grease. This low drag will help prolong motor life, reduce energy consumption, reduce wear on drive gears & chains, and help keep your facility up and running even in the most severe cold weather!
Radiation Conveyor Systems
Many products are required to be sterilized for safety purposes. Cosmetics, baby products, fruits & vegetables, spices, medical devices, etc. are just some of the products regularly sterilized. Three popular ways to accomplish this are: chambers pressurized with EO (ethylene oxide); conveyor line for EBeam (high energy focused electron beam); and conveying product over a radiation (Cobalt 60) source. The Ebeam & radiation processes are very hard on oil and grease lubricant since they tend to vaporize off the liquid content of the lubricant leaving only the resin like residue in the wheel or bearing. CSL has proven to be the very best performing and long lasting lubricant for these markets. It has been in use in this industry for over 12 years with no failures! Maintenance of these conveyor lines regarding lubrication has been reduced to zero.
Other radiation environment applications include: robotic crawlers used to inspect areas inaccessible to humans, overhead cranes in nuclear power plants, and radioactive materials handling or processing.